Pomoćnik direktora za proizvodnju i energetiku u kompaniji „Alumina“, doktor tehničkih nauka Zoran Obrenović, kaže da je „Alumina“ jedno veliko polje izazova, navodeći tehnička poboljšanja ostvarena u proizvodnim sektorima naše fabrike u 2023. godini.
„Alumina“ je kompanija kojoj je osnovni zadatak proizvodnja vrlo različitih proizvoda iz oblasti hidrata i glinica, kao i iz oblasti silikatne i alumosilikatne hemije. Osnovni zadatak proizvodnje je svakako da pripremi i organizuje proizvodnju u traženom kapacitetu i da obezbijedi kvalitet svih naših proizvoda. U toku 2023. godine ostvaren je ukupan tehnološki rezultat od 285.200 tona i prodato je ukupno oko 387.650 tona različitih proizvoda koji danas čine proizvodni portfolio naše fabrike. Međutim, sama proizvodnja nije dovoljan garant opstanka kompanije u budućnosti. Fabrika mora stalno da radi na osvajanju novih proizvoda, kao i na optimizaciji proizvodnih procesa i poboljšanju kvaliteta gotovih proizvoda. Svjesni upravo ovih činjenica, inženjerski kadar iz proizvodnih sektora je u 2023. godini definisao i realizovao niz izmjena tehnološkog procesa koji su u dobroj mjeri poboljšali kvalitet proizvoda i ekonomiku procesa.
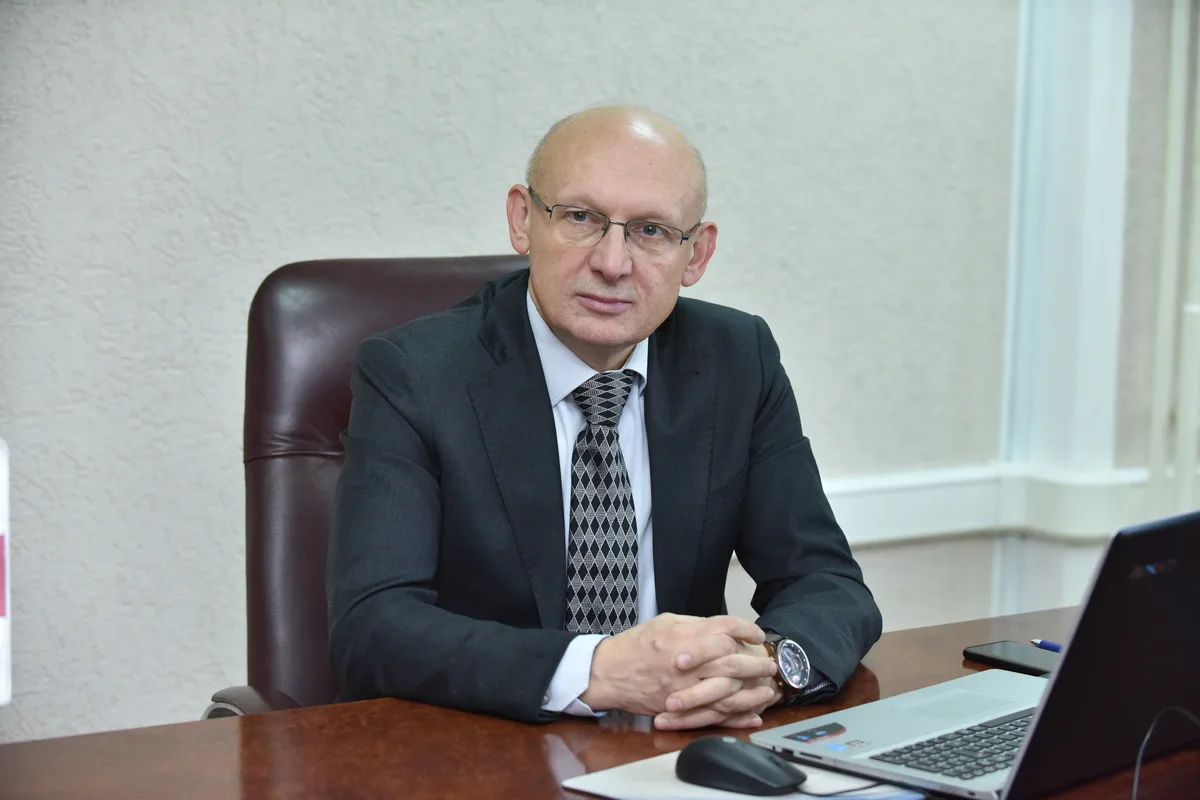
U Sektoru proizvodnje finoprecipitiranih hidrata i korunda, krajem prošle godine, zajedno sa inženjerima iz Razvoja, definisali smo tehnološke parametre i uspješno sproveli proizvodnju novog tipa finoprecipitiranog hidrata Alolt 120 F. Kako bi obezbijedili sigurniji rad opreme i osigurali bolji kvalitet gotovog proizvoda, na pogonu za proizvodnju finoprecipitiranih hidrata urađeno je nekoliko rekonstrukcija: instalacija novog cjevovoda za hemijska čišćenja opreme, instalacija novog cjevovoda za hlađenje pulpe u procesu precipitacije kao i dodatni sistem hlađenja pulpe u precipitatoru koji omogućava promjenu kinetike procesa precipitacije u cilju izmjena karakteristika gotovog proizvoda. S obzirom da je u toku 2022. godine bilo primjedbi naših kupaca po pitanju prisustva magnetičnih čestica u gotovom proizvodu, u 2023. godini izvršili smo instalaciju magnetnih separatora na pozicijama dolaska materijala u silose gotovog proizvoda, na ulazu materijala u pakirnice i na utovarnim glavama za punjenje cisterni. Na pogonu za proizvodnju korunda, zajedno sa Tehničkim biroom i Održavanjem, urađena je rekonstrukcija peći, čime su gubici glinice sa početnih 10% smanjeni na 3%. Tako se na godišnjem nivou, na punom kapacitetu peći od 6.000 tona korunda, smanjuje potrošnja glinice za oko 420 tona, čime se pravi ušteda oko 300.000 KM. Takođe, na ovom pogonu urađena je rekonstrukcija sistema hlađenja gornjeg i donjeg dijela peći i držača elektroda, čime je smanjen normativ utroška električne energije sa 1600 kWh/t na 1400 kWh/t korunda. Uz sigurniji i pouzdaniji rad peći, ova rekonstrukcija će na punom kapacitetu peći na godišnjem nivou donijeti uštedu od oko 170.000 KM.
U Sektoru proizvodnje glinice, na pogonu Pripreme rastvora, zajedno sa Istraživačkom laboratorijom i održavanjem, uveli smo novu tehnološku šemu tretmana srednjeg filtrata sa Prerade rastvora aditivom za uklanjanje organskih materija i filtraciju tretiranog srednjeg filtrata u cilju odvajanja izdvojenih organskih primjesa, a osnovni benefit je poboljšanje kvaliteta naših gotovih proizvoda u smislu povećane bjeline. Takođe, na Pripremi rastvora uradili smo izmjenu tehnološkog procesa posle kontrolne filtracije na sistemu bijelog hidrata koji ima za cilj smanjenje gubitaka lužine i glinice i izmjenu koja je uvela filtraciju pulpe posle kaustifikacije izdvojene sode. Nakon filtracije rastvora za bijele hidrate i FPH, dio korisnih komponenti lužina i glinica su završavale na brani crvenog mulja, kako je to predvidio projekat. Urađenim rekonstrukcijama smanjeni su gubici u ovom dijelu procesa za oko 80%.
Za pola godine koliko funkcioniše ova izmjena, smanjeni su gubici lužine za oko 550 tona, a glinice oko 200 tona, što uz cijenu lužine u drugom polugodištu prošle godine od 1.000 KM/t pokazuje da je napravljena ušteda od oko 650.000 KM. Isto tako, filtracijom pulpe, posle kaustifikacije, smanjuju se gubici lužine u rastvornom obliku za oko 0,5 kg/ t tehnološkog rezultata, pa i ova rekonstrukcija na godišnjem nivou pravi uštedu od najmanje 100.000 KM. Na Preradi rastvora uradili smo drenažni sistem ispod dekompozicije i stabilizovali granulometriju na bijelom hidratu. Drenažni sistem na dnevnom nivou pravi uštedu lužine oko 0,6 tona, a glinice oko 0,15 tona, tako da je za pola godine koliko funkcioniše ova rekonstrukcija napravljena ukupna ušteda od oko 150.000 KM. Uvođenjem FPH kao cjepiva u sistemu bijelog hidrata smanjile su se oscilacije u pogledu granulometrije bijelog hidrata. Srednji prečnik bijelog hidrata ranije je oscilovao u intervalu od 40-60 mikrona, dok se srednji prečnik bijelog hidrata danas kreće u granicama 45-55 mikrona, čime smo pod bolju kontrolu stavili proces proizvodnje bijelog hidrata. Na pogonu kalcinisanja i sušenja hidrata urađeno je nekoliko inovativnih poboljšanja procesa: ugradnja sušača i odvajača vlage na liniji vazduha za potrebe silosa glinice (1,2,3,4), zatim je osmišljena, urađena i uvedena u rad šema vraćanja filterskih frakcija sa sušare i mlina hidrata i dijela elektrofilterske glinice u CS na vertikalnoj peći.
Na ovaj način u mogućnosti smo da bolje kontrolišemo kvalitet glinice kao gotovog proizvoda. Takođe, urađena je instalacija odvajača vlage na liniji komprimovanog vazduha za potrebe hladnjaka vertikalne peći. U konačnom, sve ove aktivnosti su preduslov za proizvodnju bijele glinice sa većim stepenom kalcinacije, odnosno sadržajem alfa faze oko 30% i proizvodnju niskoalkalne i nemetalurške glinice čija će suma vlage i gubitka žarenjem biti manja od 1,5%. Za oba ova proizvoda postoji ozbiljno interesovanje tržišta. I na kraju, u prethodnoj 2023. godini, na linijama suvih hidrata i glinica, ugrađeni su magnetni odvajači, koji su se pokazali veoma efikasnim u uklanjanju magnetičnih čestica, čime se smanjuje nivo primjesa i unapređuje kvalitet naših proizvoda.
Na pogonu za proizvodnju silikagela u prethodnoj godini osvojena je tehnologija za proizvodnju novog silika gela SG-560 sa značajno manjim sadržajem metalnih jona. Sadržaj Ca je manji od 80 ppm, sadržaj Fe je manji od 50 ppm i sadržaj Na je manji od 300 ppm. Pored toga, uvođenjem “duplog moda” na reaktorima koji je podrazumijevao izmjene u sintezi silikagela i rekonstrukciju opreme reaktora, povećan je kapacitet proizvodnje silika gela. Tako je 2019. godine proizvodnja silika gela na četiri reaktora bila oko 300 tona, dok je 2020. godine proizvodnja bila na nivou od 560 tona. U 2023. godini na četiri reaktora imali smo ukupan kapacitet proizvodnje od 730 tona silika gela.
Na ovaj način stručni kadar je pokazao da zna i da može da upravlja tehnološkim procesima i da se može nositi sa svim izazovima u budućnosti. Na njih se ozbiljno treba računati. Sva navedena poboljšanja proizvodnih procesa rezultat su isključivo domaće pameti. Fabrika je jedno veliko polje izazova, gdje se može puno naučiti i gdje ima zaista puno prostora za ličnu i stručnu afirmaciju i dokazivanje, zaključuje na kraju dr Zoran Obrenović, pomoćnik direktora za proizvodnju i energetiku u kompaniji „Alumina“.